Production process development
When you need competence and tools for developing your production, productivity or operative operations, we help you find the solutions through consultation and development work.
- Application and introduction of lean methods
- Improving the efficiency of the logistics and material flows of the factory
- Utilization of simulation in production development
Production development can be strategic work to improve your production strategy or it can be striving towards continuous improvement and looking for ideas to find new solutions. The work can be based on improving the productivity or adjusting the performance of the product selection so that it matches the demand in the market.
Typically, the work begins with workshops where we map out the challenges, objectives and the methods and training needed, which we then tailor to the needs recognized. After the workshops, we can move on to introducing the achieved improvements and development ideas in the operative operations of the factory.
Development workshops
- Tailored workshops based on customer industry knowledge
- Training sessions on Lean and Factory Physics
- Topics can vary from specific production problem solving to strategy and action plan development
- Group working method based on Lean
Do you need consultation for investment planning and operational improvement? We organize facilitated workshops to solve different problems concerning production development.
We always tailor our development workshops according to your needs. Typical topics and problems include factory, line and machine concepts, investment planning and operational performance improvement (e.g. Lean).
The aim is to solve bottlenecks that prevent development, and to provide a viable solution to the problems at hand. We also aim to plan activities that improve your operational performance.
We use different teamwork methods and facilitate workshops to ensure that we achieve the best solution to your challenges. Therefore, experts also from other Elomatic domains might take part. Typically, the workshop team consists of 3–10 key people from your side, plus a coordinator and experts from Elomatic.
Most often, 5-8 workshops are needed, depending on the complexity of our task.
Lean manufacturing
- With our workshop methods, we can develop a common perspective on the implementation of the Lean method
- With Lean methods, we can help you with productivity, delivery times and delivery reliability
- Lean methods often require change management, in which we can help you by identifying different roles and competences in your company
Lean ideas and tools are often easy to understand, but in most companies, hard to implement. We help you to identify which Lean methods best support your production process.
At the core of Lean thinking is the concept of waste, which can include unnecessary movements, inventories, work in progress and waiting. Lean can be summarized as an operations strategy that prioritizes efficient production flows over utilization rates.
We at Elomatic have identified the most common problem with Lean: It has not been incorporated into operations to the extent it would bring noticeable improvement in productivity. Usually, this is due to lack of understanding of which Lean tools to implement, in which order and how much time these operations take.
When you wish to gain a competitive advantage from Lean, it needs to be seen as continuous activity with allocated resources – rather than a project with a start and an end. We can help you with creating Lean culture, and identifying how much knowledge and human resources the Lean method requires. We also help you to put Lean principles into practice.
Layout development
- Scope, content and level of details defined based on your project’s needs
- EIA and HVAC can be included in layout planning
- Safety analysis on material routes and walkaways
- Phase-by-phase approach often adopted
Working layout is a backbone for all well operating factories. With it, you can ensure efficient and safe material flows along with the right located and sized buffers and storages.
Whether you need help with layout development on the work cell, line or entire factory level, we are here for you. Your project might include improvement of existing layout, or it might as well be part of an investment plan.
We can support your layout development with various tools, which include process charts, simulations, Lean considerations, development workshops and 2D or 3D modelling tools. We also design internal traffic with material and personnel walkways, as well as appropriate safety regulations and methods.
Quite often we also collaborate with building and construction parties, as well as machine suppliers.
Contact us
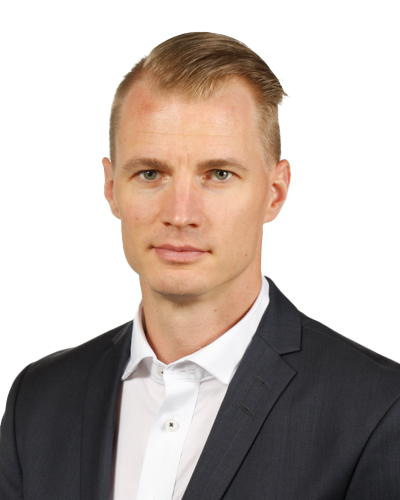