Elomatic implemented a new heat pump system for Valio’s Seinäjoki plant – utilizes waste heat and brings significant savings
CLIENT
Valio
PROJECT
A heat pump system was implemented at Valio’s Seinäjoki plant to capture waste energy streams from factory processes using four new heat pumps. The new, more energy-efficient system aims to achieve annual heating savings of 12–14%.
TIMELINE
Design of the heat pump system began in 2021, and the new system was commissioned in the fall of 2023.
OUR ROLE
Elomatic, in collaboration with Valio, carried out the concept and implementation design for the new heat pump system. The project included process and plant design, electrical and instrumentation design, and CFD-analysis. Elomatic also consulted Valio on project procurement.
“It was important for us to find a partner who could, in addition to project implementation, perform the necessary field measurements to refine the sizing of the new system. Our collaboration with Elomatic has been smooth.”
Jussi Jääskeläinen, Energy Specialist, Valio
How did we do it?
The heat pump facility modernization project began with factory-wide energy measurements and analyses. This assessment identified the waste heat sources at the factory, which allowed the heat pump system concept to be designed and properly scaled.
An essential part of optimizing the heat pump facility’s efficiency was increasing the operational hours of the heat pumps. By analyzing collected data, the design aimed to optimize both heat recovery and distribution to improve energy efficiency.
According to Elomatic’s Project Manager, Henri Antikainen, thorough analysis is key in energy efficiency projects: “Drawing the right conclusions is challenging. A precise analysis phase is essential to designing effective solutions that drive energy efficiency and savings.”
The new heat pump facility was upgraded with a heat recovery system, a heat storage tank, and heat pumps. A challenging aspect of the redesign project was that the new system was partially designed and built alongside the existing system, and construction and dismantling had to be done to minimize production impact. With careful planning, the new system was built and the old one dismantled while keeping the production downtime as short as possible and well-scheduled.
In addition to enhancing energy efficiency, the project also improved the environmental sustainability of the entire heating system by replacing the previously used refrigerant with ammonia. Ammonia has a GWP (Global Warming Potential) of zero, meaning it does not contribute to climate change.
Contact us
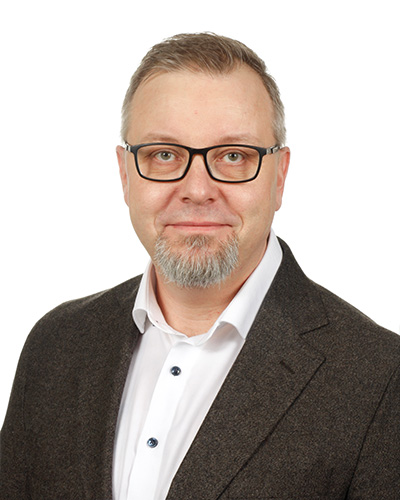
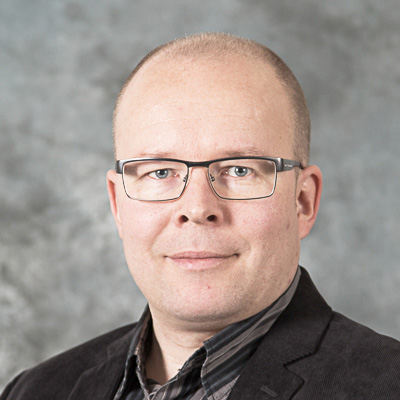