Computational fluid dynamics in aerodynamic and lightweight structures
If you are looking for an expert in computational fluid dynamics, we are the right partner for you. Our team represents the cutting edge of research on aerodynamic and lightweight structures in Finland.
- Aerodynamics
- Airplane simulations
- Finflo
- Fluid–structure interaction (FSI)
When compared to many industrial application, aerodynamic applications are challenging due to the fact that the friction, or the boundary layers, must be solved with precision. For this reason, we use both commercial CFD codes and our own CFD code, as the work requires extreme precision.
Compared to the commercial codes, it is easier to rely on the results given by our own meticulously selected code. It is also easier to make case-specific changes to it if necessary.
Aerodynamics – Fluid structure interaction
- Aerodynamics
- Hydrodynamics
- Fluid structure interactio
Some of the processes or devices need combination of computational fluid dynamics (CFD) and structural analysis (FEM) for the simulation. The method is called fluid structure interaction (FSI).
Aerodynamics or hydrodynamics can impact the structure with elevated pressure loading the structure or with thermal conditions contributed. In some cases, the structure can be deformed to the extent that it impacts the flow conditions.
A carefully planned and executed study combining computational fluid dynamics (CFD) and structural analysis often results in more functional devices with optimal performance.
One example of a case in which fluid structure interaction can be used in simulation is a high-speed paper mill: it is a device where the pressure levels contributed by air stream have an impact to the position of the paper, and on the other hand, the position of the paper impacts the air stream.
Acoustics simulations
- Gear noise
- Fan noise
- Cabin noise
- Underwater acoustics
- Flow induced noise
- Meeting environmental standard
Acoustic simulations include analysis of noise generation and propagation. The noise generation is most often related to product development, while propagation requires environmental analysis.
Noise generation is often an environmental issue – however the high noise production is mostly a sign of low product efficiency. Thus, improving product performance usually leads to lower noise levels as well.
Noise production can be simulated, for example, in cases where turbulence fluctuation or a movement in a mechanical structure contributes to acoustic waves. Quite often it is seen that these two are combined and related to reactions or phase changes during the process.
One example of the applications is propeller-induced underwater noise, where the noise sources are pressure pulses, turbulence from blades and cavitation from tip vortex. The analysis with computational fluid dynamics (CFD) helps to find the reasons for noise generation in the design. This will help to find less noisy design alternatives, which often are more efficient as well.
For noise propagation, we frequently apply both low frequency analyses (using the finite element method, FEM) and high frequency analyses (using statistical energy analysis, SEA).
Mathematical modeling and physics coding
- Mathematical modeling
- Physical modeling
- C++
- Python
- Fortran
- Matlab
- User defined functions
Mathematical modeling and physics coding enable simulation of exotic processes or devices, whose physics might not be implemented in existing codes available.
It is not always possible to use commercial simulation software when dealing with complex processes and spearhead technologies. In case of very high computational costs, a customized semi-empirical fit may decrease the computational burden significantly, thus making the project economically feasible.
We can customize existing models, fit empirical sub-routines, make user interfaces or code brand new physical phenomena. The tools we normally use include C++, FORTRAN or MATLAB. Our mathematical models are usually used as a part of the commercial CFD solvers or in-house CFD code FINFLO®.
We also have extensive experience of programming user-defined functions (UDF) for ANSYS Fluent.
Special know-how
- Mathematical modeling
- Physical modeling
- C++
- Python
- Fortran
- Matlab
- User defined functions
Our special know-how includes codes for exotic physics not implemented in commercial codes available. We develop and tailor these codes to enhance and supplement commercial software according to your specific case.
Some of the applications require specific methods or mathematical models to analyze. However, the subroutines developed for specific physics can be included in the fluid dynamics simulations. They can then be connected to structural analysis as well to allow complex physics simulation with high precision.
We have developed, for example, methods to simulate water bentonite flow dynamics, noise production with cavitating propellers or blood flow in human vessels – and many other special and demanding applications.
Contact us
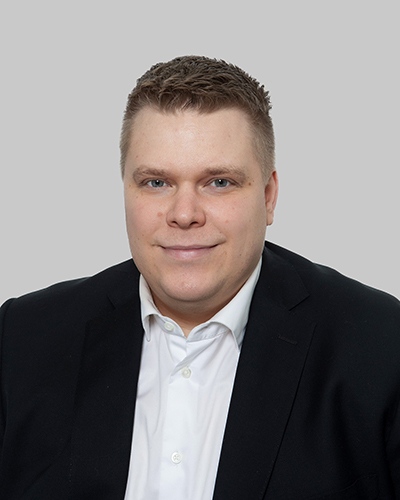