A transformative shift in the pharmaceutical industry:
Resource efficiency with single-use equipment
Author: Mona Åkerholm
Estimated reading time: 4 minutes
In recent years, the global pharmaceutical industry has faced increasing pressure to minimize its environmental footprint while maintaining the highest standards of product quality and safety. One innovative approach gaining traction is the adoption of single-use equipment in pharmaceutical production processes. This shift not only enhances efficiency and flexibility but also significantly reduces resource consumption and waste generation.
Listen to the article
Traditional pharmaceutical manufacturing relies on stainless steel equipment that requires extensive cleaning, sterilization, and validation between batches. This process consumes substantial amounts of water, energy, and chemicals while generating significant wastewater and carbon emissions. Additionally, the long lead times and high capital investments associated with stainless steel equipment can hinder agility and scalability in production.
By contrast, single-use equipment offers a compelling alternative. These disposable components, such as bags, filters, tubing, and connectors, are designed for one-time use and then safely disposed of or recycled. This eliminates the need for cleaning and sterilization, streamlining production workflows and reducing downtime between batches. Moreover, single-use systems are modular and scalable, allowing pharmaceutical companies to adjust production capacity more rapidly in response to market demand.
Traditional stainless steel systems require large quantities of water for cleaning and sterilization, contributing to water scarcity and wastewater pollution.
Let’s take a closer look at how adopting single-use equipment can pave the way for a more sustainable future in pharmaceutical manufacturing.
Reducing resource consumption
One of the most significant advantages of single-use equipment is its ability to conserve resources throughout the production lifecycle. Traditional stainless steel systems require large quantities of water for cleaning and sterilization, contributing to water scarcity and wastewater pollution. By transitioning to single-use solutions, pharmaceutical manufacturers can drastically reduce water consumption, alleviating environmental pressure and minimizing operational costs.
Furthermore, the energy-intensive nature of stainless steel processing contributes to greenhouse gas emissions and climate change. Single-use equipment requires less energy for operation, as it eliminates the need for heating, cooling, and running complex cleaning cycles. This results in lower carbon emissions and a reduced environmental footprint, aligning with global efforts to combat climate change and promote sustainable practices.
Impact of single-use equipment on waste reduction
Another compelling benefit of single-use technology is its ability to minimize waste generation throughout the manufacturing process. Stainless steel equipment generates significant quantities of wastewater and chemical waste during cleaning and sterilization cycles, posing environmental risks and disposal challenges. In contrast, single-use components are disposed of after a single use, reducing the volume of waste generated and simplifying disposal procedures.
Moreover, the modular design of single-use systems enables more precise control over material usage, minimizing overages and reducing the likelihood of product loss or contamination. This not only enhances product quality and safety but also optimizes resource utilization, maximizing efficiency and cost-effectiveness in pharmaceutical production.
Single-use systems offer inherent advantages in terms of sterility and cross-contamination control.
Opportunity for designing modular cleanrooms
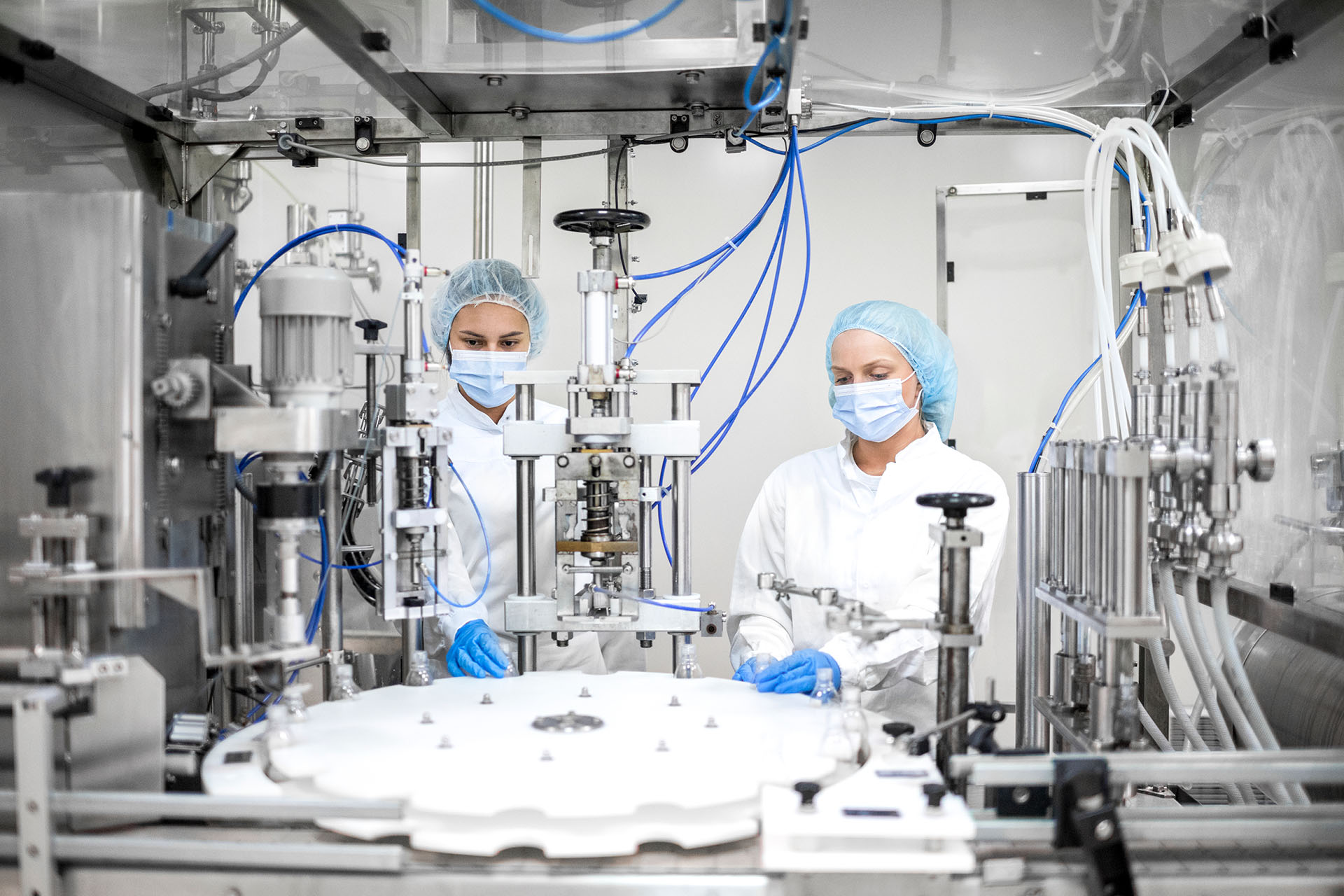
Single-use equipment usually requires a smaller footprint in the manufacturing suite. A smaller footprint makes it possible to design and deliver modular cleanrooms. Modular cleanrooms can be manufactured at the factory and require only a small amount of installation work at the site.
For example, the Naya Cleanroom factory mainly runs on solar energy, and its production aims to minimize and reuse the waste generated. Less traveling for installation and shipment to the site will add to the decreased impact on the environment.
The largest energy consumers in a pharmaceutical manufacturing suite are the ventilation and the generation of clean utilities. The smaller footprint of the cleanrooms decreases the needed amount of air circulated, and smaller consumption of clean water and steam will decrease the energy needed for producing them. Energy-efficient production is crucial for the sustainability of the pharmaceutical industry.
Ensuring compliance
One common concern associated with single-use technology is its impact on regulatory compliance and product quality. However, modern single-use systems undergo rigorous testing and validation to ensure they meet the highest standards of safety, purity, and performance. Regulatory agencies, such as the FDA and EMA, provide guidelines and requirements for the implementation of single-use technology in pharmaceutical manufacturing, ensuring adherence to Good Manufacturing Practices (GMP) and other regulatory standards.
Furthermore, single-use systems offer inherent advantages in terms of sterility and cross-contamination control. With disposable components, the risk of microbial contamination is significantly reduced, enhancing product integrity and patient safety. Additionally, single-use technology enables more frequent equipment changeovers, minimizing the potential for product carryover and ensuring batch-to-batch consistency and reproducibility.
Empowering sustainability
The adoption of single-use equipment offers a sustainable solution to resource conservation, waste reduction, and operational efficiency. By embracing single-use technology, pharmaceutical manufacturers can minimize their environmental footprint, enhance regulatory compliance, and deliver high-quality products to patients worldwide.
As the industry continues to evolve, the widespread adoption of single-use systems will play a pivotal role in shaping a more sustainable future for pharmaceutical manufacturing.
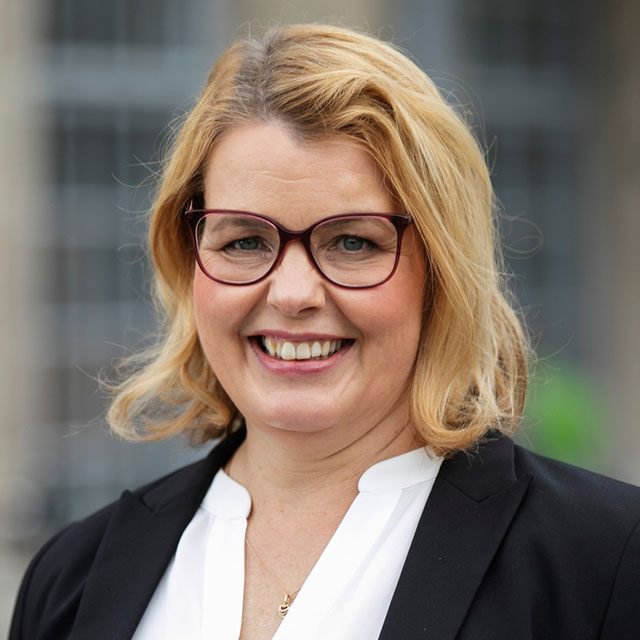
Mona Åkerholm
M.sc.,
eMBA, IPMA B, HHJ
Mona oversees the Pharma business unit at Elomatic, leading a team of 200 professionals with vast expertise in engineering, project management, and consulting for the pharmaceutical industry. Mona has worked in the industry for 25 years, primarily focusing on the execution of small and large-scale investments.
mona.akerholm@elomatic.com
Want to know more? Check out these related articles:
Energy efficiency in cleanrooms – Dangers of overdesign or under-design
Since the global energy crisis hit, companies in pharmaceutical manufacturing started improving their energy efficiency to contribute to the economy as well as to their budget. Heating, ventilation, and air conditioning (HVAC) systems are typically the biggest energy consumers in pharmaceutical facilities, and design is the best stage at which to influence them.
EloTalk: What is the role of engineering in fostering a more sustainable pharmaceutical industry?
The discourse surrounding sustainability and ethical considerations is increasingly gaining prominence within the pharmaceutical industry. Environmental concerns underscore the significance of minimizing wastewater and curbing emissions in this sector. To foster a cleaner operation and guarantee sufficient medicine availability for all, what measures must be taken within the industry?