07/06/2023
Saving energy by reducing weight—advantages of structural analysis using modeling
As the price of energy is rising, so is the price of materials. That is why it is now worth reducing the weight of structures to save energy and money. Structural analysis using modeling offers great opportunities here: the models give better results on the details of the structure, and thus the material can be used where it is needed. In addition, models help in choosing the right materials and in extending the service life of structures.
Recently, there has been a lot of talk about the CO2 emissions of different materials and applications and how to reduce them. Lately, the discussion has shifted more to energy consumption and how it could be reduced.
This article concentrates on the possibilities of reducing energy consumption using structural analysis, especially the finite element method (FEM). With possibilities to save not only energy, but also time and money, structural analysis should not be ignored at any design stage.
Benefits of modeling are undeniable
Over the years, structural analysis has moved from using purely manual calculations to more and more sophisticated models. Analytical models are fast and reliable but cover only specific cases and thus restrict the design.
As computational power has increased and modeling tools have become more advanced, making complex models has become more common for different applications. These models can be used to analyze the strength and behavior of a structure.
FE models give better results on the details of the structure, and thus the material can be used where it is needed. For example, instead of making the whole bulkhead of a boat thicker, the thickness can be added to specific locations, and fatigue can be prevented with some carefully placed brackets in the corners. Another benefit is the possibility to change the thickness or material parameters easily.
The right materials offer a huge reduction in weight
Weight saving is not achieved only by optimizing the amount of material used or the type of steel, but also the material itself. Frequently used alternatives to steel are aluminum and composites. Aluminum is three times lighter than steel, although its strength, fatigue life, and weldability properties are poorer. Composites are also very light and can offer a huge reduction in weight, up to 50–70%1. One of the problems with composites is manufacturing quality.
Modern modeling tools give the possibility either to model composites as layers or to estimate the properties of a relevant corresponding heterogenous material. The latter makes it possible to have approximate estimates of the suitability of the composite.
Significance of structural analysis is emphasized in moving machines
In moving machines, such as cars or elevated work platforms, conserving energy by conserving weight has been an industry practice for a long time. For example, the automobile industry uses composites for many parts to reduce weight. A 10% mass reduction results in approximately a 6–7% energy reduction when moving the vehicle1.
High-strength steels with tensile strength even over 1000 MPa are also becoming a more and more frequently used solution when trying to save weight. Using structural analysis, it is easy to find the minimum sheet thickness needed, depending on the strength of the steel used. This makes it easy to estimate both financial and energy savings when changing the material.
Welding these high-strength steels is more challenging, as the risk of distortion is larger than for conventional steels. This risk can be reduced through modeling the welding process, for example to optimize the welding sequence.
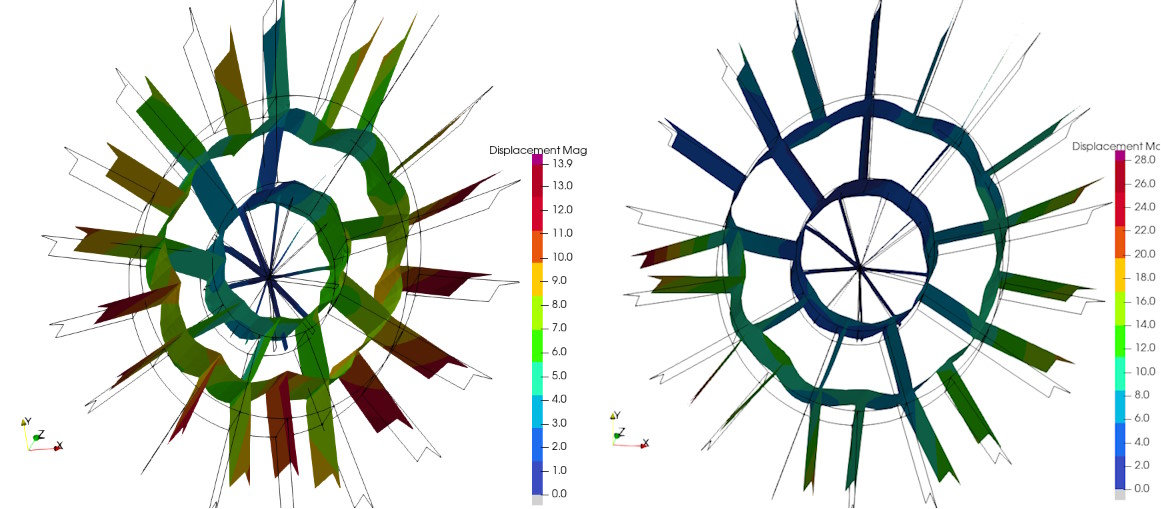
The energy used by material manufacturing also matters
Material manufacturing plays a big role in the energy consumption of structures, especially for stationary solutions, where weight has not traditionally played a big part. In Finland alone, the metal manufacturing and refining industry uses 13% of the energy consumption of the whole industry sector, which amounts to 17 TWh a year2. Energy consumption accounted for 10–40% of the manufacturing costs of the metal industry in 20172.
As the price of energy is rising, the prices of metals are fluctuating, depending on demand. The price of steel in the US grew by 200% between March 2020 and July 2021. Estimating the future price is difficult, but this risk can be reduced if less material is needed. Globally, the steel and iron manufacturing industries use 98 000 TWh in a single year3. Even a small reduction in the amount of steel and iron needed would mean a huge amount of saved energy.
However, composites or aluminum are not the solution to this problem, either: the energy consumption required to manufacture carbon fibers is even greater than for metals. Therefore, substituting steel with carbon fiber or aluminum as a means of saving energy is valid only when the energy saving takes place throughout the entire life cycle of the structure, as with moving machines, not just during the manufacturing phase.
Material | Energy intensity |
---|---|
Steel4 | 31–34 MJ/kg |
Carbon fiber5 | 198–595 MJ/kg |
Aluminum4 | 200–220 MJ/kg |
Steel recycled4 | 7.7–9.5 MJ/kg |
Aluminum recycled4 | 22–30 MJ/kg |
Modeling also helps in extending lifetime and reducing energy loss
As manufacturing new products takes a lot of resources and energy, extending the lifetime of existing structures is important. The models and methods available today for structural analysis are more sophisticated and can give more precise predictions for fatigue life. Combined with 3D scanning, this enables the assessment of the factory’s remaining lifetime to be extended from the original estimate.
Yet another way to utilize modeling is to reduce direct energy loss with it, for example by modeling heat transfer problems. Optimizing the amount of insulation needed can reduce both the amount of material needed and the energy loss experienced.
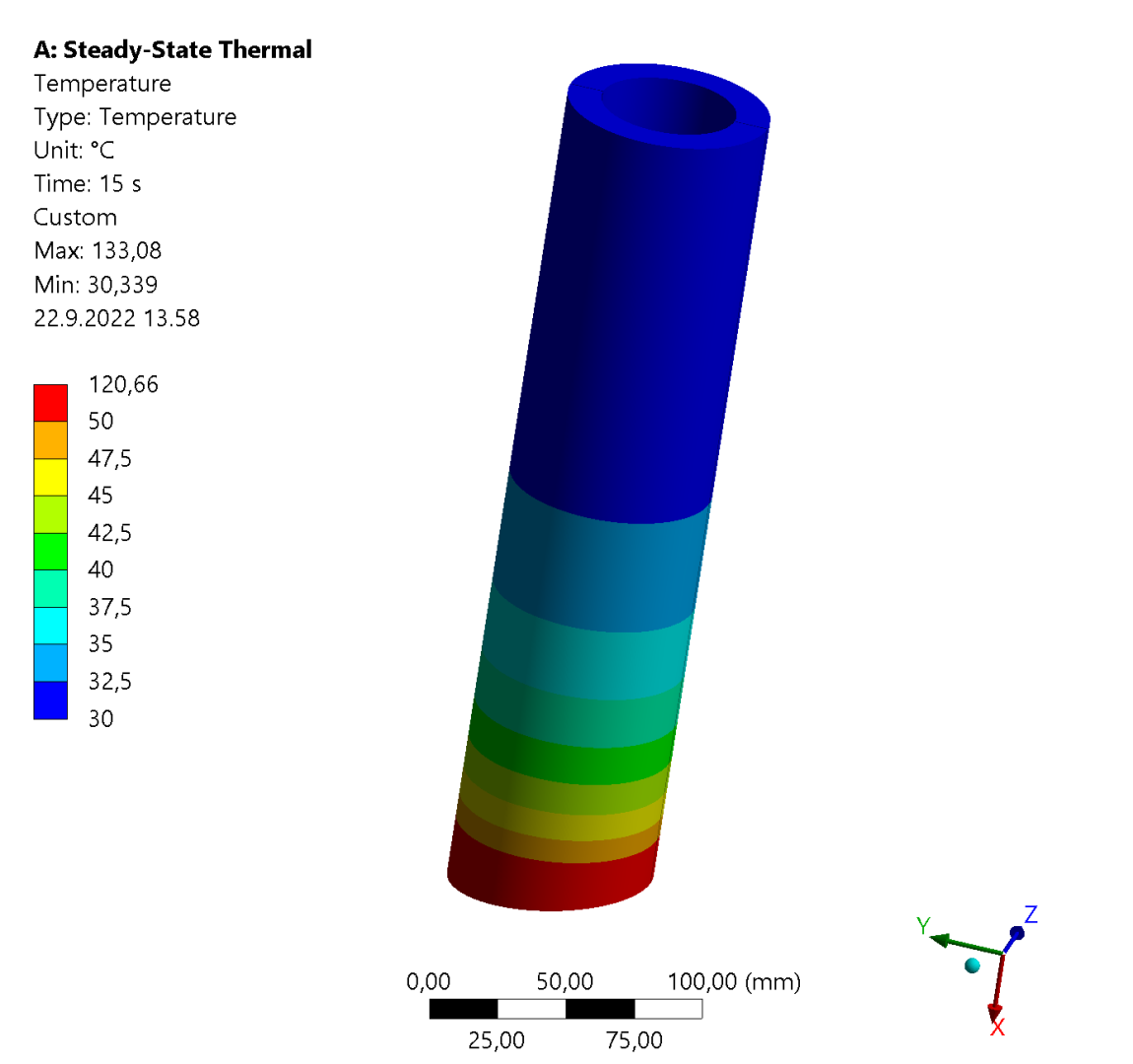
Sometimes the best option is to start with novel concepts
Although energy is just one parameter, finding the best ways to save it is a complex multiple parameter problem. It is not a simple task to find out where energy consumption occurs and where the greatest opportunities for savings are. Structural analysis and modeling can help with identifying some of the parameters and estimating where the biggest savings can be found.
One method is to test completely new concepts that can perform better or that are significantly lighter than other currently used structures. This is where structural analysis and models bring a huge advantage: models make it easy to test different ideas and to compare varying concepts with each other. In this way, the best ideas can be found early in the design process.
References
- Vehicle Technologies Office, ”Lightweight Materials for Cars and Trucks,” Office of Energy Effeciency and Renewable Energy, [Online]. Available: https://www.energy.gov/eere/vehicles/lightweight-materials-cars-and-trucks. [Retrieved September 2022].
- Työ- ja elinkeinoministeriö, ”Energian kulutus ja sähkön hinta metallinjalostusteollisuudessa,” Työ- ja elinkeinoministeriön julkaisuja, osa/vuosik. 15, 2017.
- IAE, ”Energy consumption in the iron and steel sector by scenario,” October 2020. [Online]. Available: https://www.iea.org/data-and-statistics/charts/energy-consumption-in-the-iron-and-steel-sector-by-scenario. [Retrieved September 2022].
- Cooper and T. Gutowski, ”The Environmental Impacts of Reuse, a review,” Journal of Industrial Ecology, osa/vuosik. 00, 2015.
- Zhang, V. S. Chevali, H. Wang and C.-H. Wang, ”Current status of carbon fibre and carbon fibre composites recycling,” Composites Part B: Engineering, osa/vuosik. 193, 2020.
Johanna Sjölund graduated in nanophysics from the University of Turku in 2008, after which she worked as a researcher at Aalto University. There she produced a doctoral thesis on the modeling of wood, which she defended in 2015. After the PhD, she moved on to consulting, first at Process Flow and since 2017 at Elomatic. She has worked with different types of projects in structural analysis, ranging from marine applications to cranes, and from high-strength steel to soft soil. Since 2021, she has been the manager of the structural analysis team in Turku and Espoo.