”
Digitalization will take resource efficiency to a new level
Marko Jaakonmäki
Elomatic’s visualization team leader Marko Jaakonmäki sees digitalization as a key factor in moving towards a carbon-neutral circular economy. He predicts a new divide in the industry: companies that can quickly adopt new technologies will thrive, while those with low levels of digital maturity will lose market share.
You have been working at Elomatic for 22 years. What has kept you here for so long?
I have always been given interesting tasks, and they have also changed every two to five years. In a way, I have had several careers within the realms of mechanical design, people management, and business development during my time here. Also, my supervisors have always been good, and I have tried to pass on the same mentoring approach by teaching young engineers and supporting their progress. I am not afraid that one day they will replace me, but I even hope that one of them will advance in their career higher than I have.
What developments do you anticipate in industrial digitalization in the near future?
At the moment, there are tremendous leaps in artificial intelligence. Generative AI is evolving faster than any technology has ever evolved and is about to start developing itself. I believe a major background factor in this is the development of quantum computers, and their computing power is already huge. According to some studies, they may be available to consumers in five to seven years. Just by combining these two technologies, you can create tremendous scenarios.
This inevitably leads to a redistribution in the industry: companies that agilely adopt new, disruptive technologies will capture even larger shares of their business sector. In contrast, companies with very low digital maturity will lose market share and eventually wither away.
What do you think about the development of the industrial metaverse?
In practice, all cloud-based business is metaverse business, and it will grow as companies rapidly move their data to cloud servers. Metaverse business was expected to grow with XR technologies on the consumer side, for example by Apple and Meta, but this has not yet happened.
According to several estimates, metaverse business will start to grow in the coming years through the industrial metaverse. Companies will begin to utilize data transfer, analysis, and simulation more effectively to maintain their competitive advantage. It is also predicted that new, previously unreachable sources of value will be found in cloud services by combining point cloud, 3D and other data sources.
There is now a major shift in industry towards a carbon-neutral circular economy. How does it manifest in your work?
First of all, it is evident that in the EU area, regulation governs energy policy and carbon dioxide emissions are now being reduced by all means. And even though this may not be visible in the work of our 3D artist, it is visible on my desk: I have to carefully look at how legislation affects our work.
In addition, many startups in the renewable energy sector approach us now with visualization requests. We assist them in persuading investors of their novel technologies by digitally bringing their innovations to life.
A really big theme that affects many global companies is how people are transported around the world. Work is increasingly moving towards remote work, and virtual environments are good tools for that. We can use them to support our customers in, for example, reducing air travel. Gradually, companies are also adopting virtual prototypes, or digital models, to increase productivity in manufacturing, installation, and logistics operations.
According to several estimates, metaverse business will start to grow in the coming years through the industrial metaverse.
Could you elaborate further on the benefits that digital models provide?
Digital models enhance business visibility as data is retrieved from machines to cloud servers for analysis using machine learning and artificial intelligence. This improves transparency and facilitates decision-making by simulating the impacts of different decisions on production and overall operations.
Virtual factory prototypes enable testing of factory operations already during product development, leading to reduced time-to-market and overall costs. This was previously either impossible or prohibitively expensive. Additionally, digital factories enhance equipment usage and safety, eliminate errors from processes, and ease factory deployment and production optimization.
Our product, Virtual Factory, provides a comprehensive overview of processes and a visual twin to support all operations: from safety management and maintenance to tendering, change implementation, and training. The aim is to enhance business autonomy and productivity by assigning machine tasks to machines and human tasks to humans, such as overseeing and problem-solving.
Can you give an example of how digital models help improve resource efficiency?
They help identify bottlenecks in a company’s operations and processes, which can be optimized to improve resource efficiency. In practice, digital models enable automatic monitoring of safety deviations. For example, an unforeseen disruption in a paper machine situation costs enormous sums when trying to determine the cause and production stops.
With the Virtual Factory model, the fault notification includes information about the location of the faulty valve, the storage location of the spare part, and the correct maintenance manual. Once sufficient data has been gathered, AI can predict potential disruptions before they occur, offering users guidance for proactive control or scheduling maintenance.
In the future, even greater value will be derived, particularly through the convergence of simulations, data, and 3D models, leading to the emergence of new types of reactive 3D simulation models. These models will be instrumental in optimizing energy consumption, reducing carbon dioxide emissions, enhancing resource management, and maximizing economic profitability.
I also see a threat in the increasing power of multinational corporations. Some companies are already more influential than small countries.
In the future, it will even be possible to develop digital twins of factories. What additional value do they provide?
According to Nvidia’s prediction, every factory will have a digital version. Such a digital factory can contain all the data related to the company’s operations, and its business benefit will be enormous because all business processes can be intersected through digital twins.
Through data intersection, a situational understanding of the process is created, which identifies business pain points. With simulation environments and more transparent business, product development solutions and the effects of factory changes can be tested before the changes are implemented. This also shows where the next bottleneck is likely to occur.
What threats do you see in the development of digitalization?
As the computing power of quantum computers grows, the level of cybersecurity deteriorates, as previously unbreakable encryption can be broken. Cybercriminals, together with high computing power and advanced AI, are worrying. Of course, companies’ cybersecurity is also developing in the same way, but some companies are falling behind in this development.
I also see a threat in the increasing power of multinational corporations. Some companies are already more influential than small countries. For instance, companies like Tesla, Google, and Meta have established their own AI divisions. Should they attain a dominant position, it would profoundly influence the competitive landscape.
All of this raises big questions: Who will own AI in the future and who will be allowed to use it? At what level will all this happen? A large part of companies don’t have the capability to use digital technologies in their operations, let alone disruptive technologies.
What innovations do you expect to see in the industry in the coming years?
I anticipate a surge in the adoption of robotics and AI within factories, leading to heightened human-machine interaction. Tesla, for instance, has already introduced a humanoid robot, albeit one without communication capabilities. As technology advances, the collaboration and communication between humans and robots are poised to reach unprecedented levels.
Factory autonomy will also increase, and employees no longer need to be stationed alongside production lines. Instead, maintenance robots and self-monitoring facilities will manage operations. Consequently, remote production work will become a viable option.
Additionally, I want to highlight the growing importance of augmented reality applications in factory environments, as the development of transparent XR glasses is now tremendous. Previously, when you put on such glasses, you ended up in a closed virtual space. Nowadays, their elements merge with the real world, offering a genuine augmented reality experience. Moreover, their usability has taken great leaps forward, and they are already very intuitive to use.
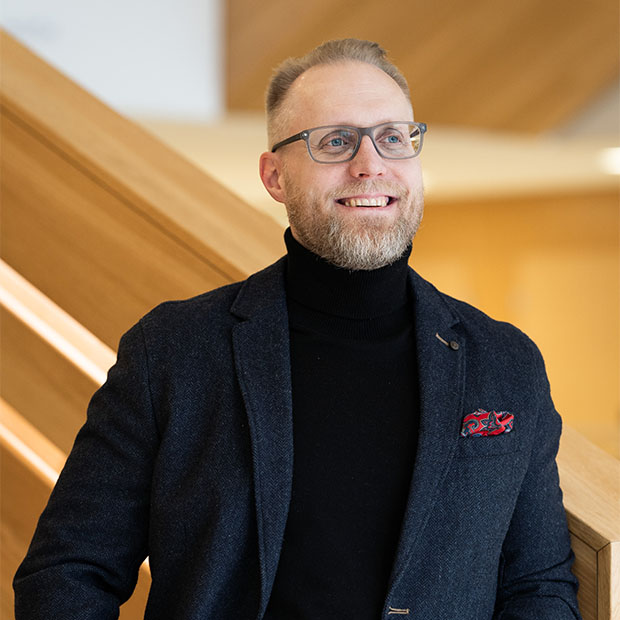
Marko Jaakonmäki
Age: 45
Lives in: Jyväskylä, Finland
Education: Bachelor of Engineering, Mechanical and Production Engineering
Employment history: From design and R&D tasks to lead designer, and then Design Manager in visualization and digital business development teams
Hobbies: Outdoor activities and fitness
Want to know more? Check out these related articles:
Striving towards Industry 5.0 – What does the future factory look like?
Many associate industrial activities with smokestacks, water pollution, and reports of factories closing due to unprofitability. In reality, industrial operations are currently undergoing a significant transformation. Digitalization is playing an increasingly prominent role in manufacturing, and clean production technologies are becoming mainstream. Innovation, especially in the fields of bioeconomy and circular economy, is thriving as raw materials and materials are utilized across industry boundaries.
How to train staff for operating a machine several hundred meters long?
The Virtual Mill virtual environment, developed by Elomatic and Valmet, enables factory workers to explore their work environments virtually. This not only facilitates training but also aids in the planning of maintenance and upgrades. Model Sachsen Papier in Germany has been utilizing Valmet Virtual Mill since the fall of 2023, with really positive feedback.